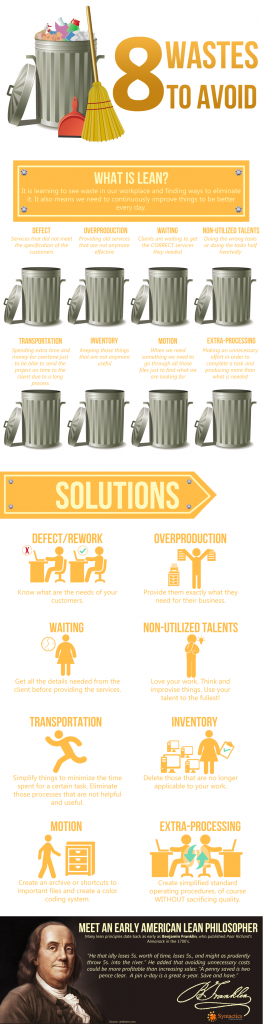
What Is LEAN and What Are The 8 Wastes of LEAN to Avoid?
You are familiar with the word “LEAN”, right? It’s the synonym of “Thin”. Do you know that we can use LEAN in our workplace? It doesn’t mean we all need to be thin. It’s something more! Want to know how?
First of all, let me tell you that LEAN is SIMPLE. It’s not complicated and you do not have to be a genius to do it. All you need to do first is to learn the meaning of LEAN.
WHAT IS LEAN?
It is learning to see waste in our workplace and finding ways to eliminate it. It also means we need to continuously improve things to be better every day.
Now, there are 8 wastes of LEAN that we need to AVOID. The acronym of these wastes is “DOWNTIME“. Yes, you read it right! So, what’s the meaning of downtime and how to avoid them?
Defect – These are products or services that did not meet the specification of the customers due to incorrect information. Defects are not only due to incorrect information, it could also be attributed to non-adherence to quality or carelessness of the person doing the work or monitoring the production. They are mistakes that require additional time, resources, and money just to fix them.
Solution: Know what the needs of your customers are. Ask them questions to be able to provide them exactly what they really want and make sure also that the people assigned to the task are providing QUALITY outputs. – No more fixes!
Overproduction – We produced so many products that are not needed at the moment and since they’ve been in the stockroom for so long, they’re starting to show some defects.
Solution: Establish a reasonable workflow for the benefit of the customers. Be sure to create a system that can immediately answer to customers’ needs – Provide them what they order in a shortest time possible.
Waiting – Customers are waiting, which is not right. They are waiting due to insufficient staffing, mismatched production rates, poor communications, very long process, work absences and fixes because of wrong products created/stocked.
Solution: Get enough staff to do the job correctly and on time. Create a faster process that still provides quality output and make sure to take all the details needed from the customer before making the products and providing the services.
Non-utilized Talents – We are not helping our co-workers or our employees use their full potential because we are making them do things that are not useful to the company, to the customers and to them. We are giving them the wrong tasks or we are not providing them enough training to learn the tasks assigned to them.
Solution: Assign employees to those jobs that you know they can excel or provide them enough resources to effectively handle the tasks you assigned them to do. Empower your employees! Don’t just tell them what to do, but ask them to think and improvised, too.
Transportation – We are transporting our products from other places due to overproduction. If we only produced what are needed there is no need to bring the finished products to the stockroom for inventory and safekeeping, but instead directly to the customer. Thus, we save time from going from one place to another and we are making a VERY GOOD customer service.
Solution: Eliminate those processes that are not really helpful. Provide what is exactly needed by our customers. Simplify things to minimize the time spend for that certain task. If something hinders you from being efficient and productive – Get rid of it or revamp it!
Inventory – Overproduction means we need to make an inventory of every finished product we have every day. We need to account each item every single day and clean them just to make sure they will remain useful when the time comes a customer would buy them. Now, that’s a waste of time!
Solution: Just produce enough to satisfy our customers. Why make many when you can just make one that the customer really want? That way, you do not have to make inventories and instead you can do other things that are needed for the moment.
Motion – Since we overproduced, our bigger place became small. When we need something we need to go through all those stocks just to get what we needed. By doing that, we are wasting time and it is slowing us down in our work by doing unnecessary work (looking/searching).
Solution: Do not overproduced to maximize your space. Make sure everything can be easily located by creating a coding/color system. Those things that are often used should be put in a very accessible place.
Excess Processing – Is making an unnecessary effort in order to complete a task and producing more than what is needed. Doing all these are just wasted money, time, effort, and resources.
Solution: Create simplified standard operating procedures, of course WITHOUT sacrificing quality.
We do not want these 8 wastes, right? That’s why we need to change our ways. We need to get rid of those wastes that are pulling us down and start doing the LEAN WAYS. We have to improve and find ways to do things that make our work easier, faster and more productive. Every day we need to continue improving things to be able to function effectively and provide more value for our customers – Not just to our customers, but to ourselves as well!
Comment 0